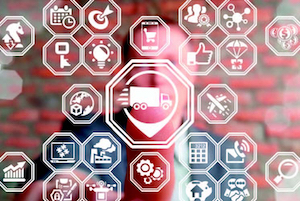
Suppliers address the complexity of supplying disposable components to the global biopharmaceutical manufacturing industry.
By Jennifer Markarian
The implementation of single-use systems (SUS) for biopharmaceutical manufacturing as an alternative to or in combination with traditional stainless-steel equipment offers advantages such as reduced capital cost, faster facility construction, and more flexible and efficient manufacturing (1). In a fully disposable or hybrid facility, however, because pieces of equipment (e.g., reactors, transfer tubing, holding vessels) are now consumables, the supply to the manufacturing facility is more complex. The demand for customized systems and the overall growth of demand for SUS add to the pressure to improve supply.
Most SUS are currently made in the United States and the European Union, but suppliers are exploring manufacturing of SUS components in Asia to serve the region’s growing biopharma market more efficiently. In September 2018, MilliporeSigma announced its first Mobius single-use manufacturing facility in Wuxi, China would begin production in 2019 (2), and in November 2018, Cytiva announced a collaboration with Chinese healthcare technology supplier Wego Pharmaceutical to produce single-use consumables in Weihai, China using Cytiva’s Fortem platform film (3). Shorter lead times are one potential benefit. Local production could also reduce the environmental impact of shipping components over long distances (4).
BioPharm International spoke with Andrew Bulpin, head of Process Solutions at MilliporeSigma; Jeff Carter, strategic project leader at Cytiva; Eric Isberg, director of Life Sciences at Entegris; and Helene Pora, vice-president of Technical Communication and Regulatory Strategy at Pall about some of the issues facing the industry as companies look to SUS for biopharmaceutical manufacturing.
Global supply chain
BioPharm: What are some of the challenges with supplying single-use systems and components globally today?
Isberg (Entegris): One area of concern is availability of customization. Large suppliers tend to focus on systems with larger quantity production, leaving short-run, highly custom systems to small boutique suppliers. Consolidation of the single-use suppliers has exacerbated this issue.
Bulpin (MilliporeSigma): Single-use supply chains are complex and dynamic. The large number of raw materials makes forecasting demand more difficult and requires robust materials management, supplier quality management, quality control, and business continuity planning to ensure continuity of supply. Common materials (e.g., silicone) are used across many vendors, which can create single points of failure within the supply chain for both the single-use supplier, as well as the end-users of their products.
The key is to adopt a comprehensive, ‘risk-smart’ approach to supply continuity and control. It is important that suppliers proactively identify the potential risks and minimize the probability and impact of supply disruptions through effective demand planning/forecasting, capacity planning, business continuity planning, change control management, disaster recovery planning, supply-chain mapping, and continuous improvement. At MilliporeSigma, a cross-functional team of subject matter experts assess risks related to demand volatility/forecast accuracy, manufacturing capacity, process and equipment, sole/single-sourced raw materials, facilities (e.g., water, utilities, power, information technology/systems), and more. Risks above a certain risk priority number are mitigated and monitored. Business continuity plans are revisited on a regular basis, and risk mitigation activities are updated continually.
Pora (Pall): Sourcing and lead times have long been challenges for both suppliers and consumers, with some of the key pain points including lead times and an ever-changing and advancing industry.
One of the most critical challenges is that biopharma is a high-risk industry. Although there have been a multitude of advances in the industry, the fact remains that the end products being made with SUS consumables are being used in humans and can mean life or death for a patient or a patient population. Even at the clinical trial manufacturing phase, a full understanding of how the process will scale is needed. Particularly in cases where high customization can be called for, the supply chain becomes more complicated and impacts the lead time.
Another challenge is just-in-time (JIT) delivery and customization. Warehousing requirements for larger spaces helps to solve storage and availability issues for off-the-shelf consumables but does not address the JIT approach or customized needs many consumers require for their process consumables.
A third challenge is that as suppliers (and the industry) evolve, product ratings, design, or supply chain sources may change, and it is critical to keep users informed. Transparency is a necessity, yet changes can impact existing processes and lead times.
As an industry, and through supplier associations like BPSA [Bio-Process Systems Alliance] and BPOG [BioPhorum Operations Group], we are working to overcome these challenges. There is a greater focus than ever on creating realistic supply-chain mapping models that address the global nature of today’s market. And a deeper importance is being placed on forecasting by end users so that the supplier and consumer can work together more effectively.
Carter (Cytiva): Issues include logistics (including time to clear customs as goods move across borders, which can counter the speed element of the single-use value proposition) and managing complaints or investigations on product that is overseas. Geographical distances and language barriers can make general communication and relationship building challenging.
BioPharm: What are the challenges/potential benefits of manufacturing SUS locally in Asia?
Bulpin (MilliporeSigma): With the establishment of manufacturing capacity and capabilities in China, we can reduce our product lead times and help our customers bring new products to market faster. In addition to shorter lead times, end-users can carry less inventory and have an enhanced level of supply security, with the ability to source their assemblies from multiple manufacturing sites.
All manufacturing sites should be working under the umbrella of a single, global quality system, and customers need to qualify the new site so that they have the ability and flexibility to receive assemblies from multiple sites
Carter (Cytiva): Proximity to a large and rapidly growing customer base does allow us to step up our service level to our Chinese customers. One practical example is the efficiency of working in native language and local time zone, particularly for configured and customized single-use systems. Developing manufacturing operations in China to complement our existing single-use manufacturing network provides an added capability in how we consider and structure contingency plans to maintain business continuity even under challenging circumstances.
Cytiva published a peer-reviewed single-use system lifecycle analysis (4). The results of this analysis showed that single-use consumables provide a better choice from the environmental impact perspective vs. the clean and re-use paradigm. The more variable aspects of the single-use lifecycle analysis and some of the more environmentally impactful elements of the value chain were the distribution of what are often large volume, low bulk-density products across various distances and transportation modes. Based on this study, localized manufacturing should have a reduced environmental impact affect; of course, there are however, diminishing returns based on manufacturing facility capacity and plant efficiency.
Pora (Pall): Over the past decade, [biopharmaceutical manufacturing] has become an increasingly global industry. With SUS, the supply chain is complicated because, regardless of the location of manufacturing, the components are often coming from different areas of the globe. Although a lot of companies are considering moving production to other locations, with Asia having particular interest, questions remain. Most critically, expertise has to be there, and an often-overlooked consideration is shipping. What will the logistics look like, and how will that impact lead times? The country that any product is manufactured in will have its own resources and regulations, which will affect the ability to industrialize production. In addition to the considerations mentioned, what is really comes down to is manufacturing in locations that have the right balance between flexibility and supply.
Quality control
BioPharm: What are some of the best practices in ensuring quality control of single-use consumables throughout the supply chain (from polymers through to the finished components)?
Pora (Pall): The best way is to have quality built in from the start. There is always going to be a need to test the end product, but it is much easier if the quality of raw materials and the manufacturing environment have already been well-considered.
There is a lot to consider when looking at the raw materials, as well. How will those impact the end product? Users want components that are animal free, and there is a long list of particulates that cannot be in there (e.g., melamine and other components). The desire for BPA [bisphenol A]-free materials is also growing.
When it comes to the process, sterilizing-grade filters can be integral for protecting quality. More attention is being paid to sterility and integrity of connections and valves and minimizing the need for operator interaction, which has a proven impact on time and safety of processes.
Isberg (Entegris): I always refer people to the BPSA quality test matrices guide (5), which is an excellent resource for quality testing for single-use systems for bioprocessing applications.
Bulpin (MilliporeSigma): Resin and film suppliers are critical to the quality control of single-use consumables. These suppliers must have a good understanding of the requirements needed for the biopharmaceutical industry, a strong quality management system, and robust change control procedures. When selecting a critical raw material supplier, partnership is paramount. You need a supplier that will grow with you, evolve, and continuously improve their process to meet the changing requirements of the industry.
Single-use suppliers should continuously monitor and mitigate risks throughout their manufacturing process to ensure a repeatable and consistent level of quality. Operational excellence and lean initiatives should be used to proactively identify areas of opportunity and prevent future errors from occurring.
BioPharm: What are some of the challenges with change management?
Carter (Cytiva): Some suppliers produce products for our industry, but their main industry is not ours. It has been observed that our industry is simultaneously a small player (in plastics) and yet among the most exacting in terms of quality requirements. Changes are common in plastics, and evaluating and qualifying these changes is resource intensive. Changes need to be managed together with our suppliers, because this can have an impact on our operations and more importantly, on those of drug manufacturers.
Pora (Pall): From an industry level there needs to be consistency in standards, including materials of construction and end products—this has to apply across the globe to be most effective. There cannot be large variations, and characterization and global agency alignment have started to play a larger role in help overcome this challenge.
Bulpin (MilliporeSigma): Change management can cause challenges for both suppliers and end-users. A large majority of single-use components are comprised of polymeric materials, and despite the high growth rates for single-use technologies over the past decade, they still make up a very small piece of the plastic consumables business. Although it’s improving, single-use suppliers still don’t have much control over raw material changes from the plastic suppliers, which means we are faced with a higher number of changes than we’d like. The volume, complexity, and cost of qualifications can be burdensome for both the single-use supplier and the end-user. With new requirements for extractables and other testing, the time associated with the assessment and qualification of changes is increasing, which makes it more challenging to manage supply risks throughout the duration of the change.
Managing change is challenging in a rapidly growing market with continuous evolving guidance that requires a smart risk-based approach. One size does not fit all. We have extensive knowledge of our customers’ processes so we can strategically evolve their manufacturing process to fit their growth plans.
References
- F. Mirazol, BioPharm Intl. 31 (2) 33-35.
- MilliporeSigma, “MilliporeSigma to Open China’s First Mobius Single-use Manufacturing Facility in Wuxi,” Press Release, Sept. 12, 2018.
- Cytiva, “Cytiva Starts to Manufacture Single-Use Consumables in China through Collaboration with Wego,” Press Release, Nov. 7, 2018.
- Cytiva, “Single-use and Sustainability,” accessed Jan. 2, 2019.
- BPSA, “Single-Use Manufacturing Component Quality Test Matrices,” bpsalliance.org